Debottlenecking separation in a gas compression train
As well as identifying the cause of performance restrictions in the configuration of the installed separators, retrofit separation internals were proposed to debottleneck each vessel. The existing equipment was evaluated using MySep software for separator rating. Retrofit internals were designed in the same separator design software and the improved performances of these proposed designs were verified by further Computational Fluid Dynamics (CFD) Modelling. Kranji also provided full retrofit engineering, procurement-guidance, inspection (FAT) and installation service.
Business Problem
A Middle East Oil & Gas operator sought our separation expertise to support a compression system upgrade project.
Gas, gathered from a number of satellite production platforms, is compressed and exported from a central processing platform. To meet the operators’ planned upgrade in gas lift demand, the customer required Kranji engineers to evaluate the adequacy of a system of horizontal and vertical two-phase separators and compressor knock-out drums with a range of separation internals devices.
The aim of the project was to achieve a very significant increase in capacity in a cost-effective way, with, limits on scheduling access to the offshore facility, access constraints for the subject separation vessels and with an aggressive project timescale
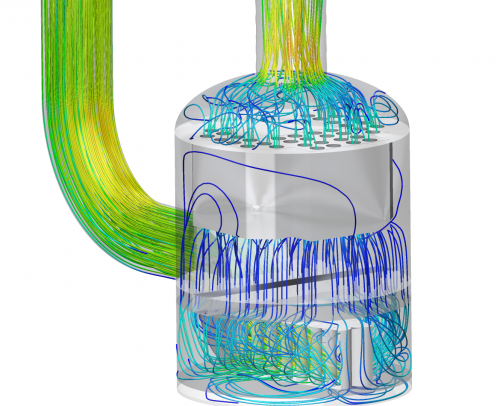
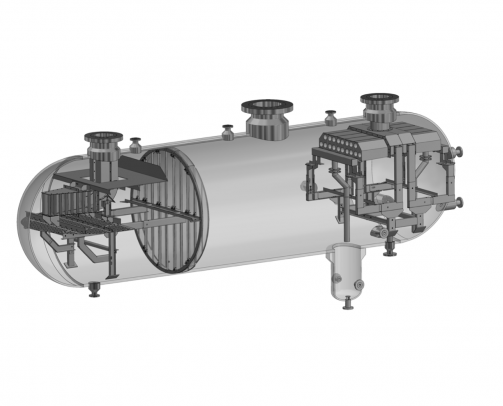
Fully Independent Analysis
Kranji Solutions operates with complete independence of separation hardware/internals suppliers. The company maintain awareness of separation technology and equipment suppliers across the globe, enabling it to recommend a short-list of reliable vendors with suitable products for any feasible separator up-grade.
MySep-Studio design and performance evaluation software was used for preliminary analyses of the existing separators prior to detailed CFD simulation. MySep-Studio was then used to develop options for retro-fit upgrade to each separator. This allowed the Kranji-team to recommend a range of suppliers for all specified internals and to impose design requirements for on-site replacement installation.
Once the customer approved the retrofit approach, appropriate CFD models were prepared to analyse the challenging conditions in these separators and KO drums. All design parameters affecting the overall performance were reviewed including:
- droplet size distributions
- mist fractions
- bulk liquid dropout
- gravity separation
- component K-values
- liquid loadings towards each component
- component performance predictions
The above considered each individual internals device including rigorous representation of demister performance entirely independent of the device supplier. The operator was provided with an accurate prediction of liquid carry-over for each separator in the system.
Solution
For each vessel or combination of vessels a suitable retrofit solution was found, reaching an overall efficiency of more than 99.9% liquid removal. The resulting liquid carry-over established was less than the common industry standard of 0.1 USG/MMSCF, ensuring trouble free compressor operations. All retrofit internals were engineered to achieve a fully bolted installation. This avoided on-site welding and post-weld heat-treatment on vessel shells, processes precluded on the operator’s offshore installation.
Once the engineering design was validated and qualified, Kranji Solutions provided a turnkey contractor service, supporting procurement, inspection and implementation of the complete retrofit internals package
Summary
Kranji Solutions provided independent adequacy checks on a system of separators and KO drums in an offshore production compressor train. Our specialist review resulted in retrofit solutions capable of meeting the desired 35% capacity increase, without the need for costly replacement of any pressure vessels. Key to success of this fast-track project was Kranji’s turnkey contractor experience of providing weld-free installations of high mechanical integrity and assured process performance.
The company’s track record demonstrates business and technical agility, identifying sources of separation internals globally, consistently delivering within severely constrained facility access, restricted physical access to vessels and with tight project deadlines.
Benefit Analysis
- Full capacity upgrade of 35% achieved
- Expert engineered solution with assured process performance
- Supplier-independent verification of performance
- Turn-key contractor service to support
- Engineering of retrofit designs
- Procurement guidance - qualified supplier short-list
- Installation & site inspection
- Fast-track completion
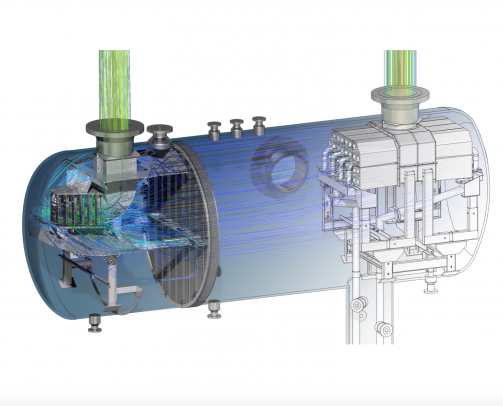
Interested?
Are you looking for troubleshooting, root cause analysis, debottlenecking or capacity increase of your equipment?