Finger Type Slug Catcher Root Cause Analysis
Kranji solutions was commissioned to undertake root cause failure analysis and a design improvement investigation on a large finger type slug catcher. Frequent liquid level alarm events resulted in plant shutdowns and consequent loss of production. Computational Fluid Dynamics (CFD) simulations were applied to model and visualize the flow distribution and performance of the unit for steady state and slugging conditions.
Kranji’s process expertise formed the basis of design improvement recommendations with operational benefit of the proposed solution being validated by further CFD study.
Business Problem
The finger type slug catcher is handling around 950MMSCF of gas per day. During abnormal operations, like pigging, peak slug loads of more than 3000m3/hr were observed. It was recognized that the operators were dealing with rapid level increases and many liquid level alarm triggers, resulting in unplanned shutdowns and control interventions. The net result was significant lost oil and gas production and reduced operating revenue.
Analysis
Computational Fluid dynamics showed a massive imbalance in liquid slug distribution between the left-hand and right-hand storage tube groupings (fingers).
Very detailed CFD simulation was undertaken including the following elements:
- Liquid flow distribution
- Gas flow distribution
- Pressure drop and pressure differences
- Transient liquid level tracking
- Droplet tracking of liquid droplets (DPM)
- Overall separation performance
Transient CFD analysis demonstrated clearly that fingers on the left of unit received around 97 % of liquid slug volume whilst those on the right received only around 3%.
Solution
The principal cause of uneven distribution in the system was attributed to asymmetry in the arrangement of inlet piping. The sub-optimal configuration biased liquid flow to the left-hand slug storage tubes.
After the implementation of improved upstream piping, a uniform flow distribution is entering both sides of the Finger Type Slug Catcher. Another modification is the introduction of an equalization line between the both liquid manifolds downstream of the liquid storage tubes. This provided further assurance that any subsequent liquid imbalance would automatically be corrected.
Summary
An unfavorable arrangement of upstream piping caused serious flow maldistribution within the Finger Type Slug Catcher. This gave rise to frequent liquid level alarm triggers and plant shutdowns, reducing productivity. The CFD and separation expertise vested in Kranji Solutions, provided a sound basis for recommendations to remedy poor distribution. Simulation of design improvements provided the client assurance of elimination of root causes and confidence that increased facility up-time would be achieved.
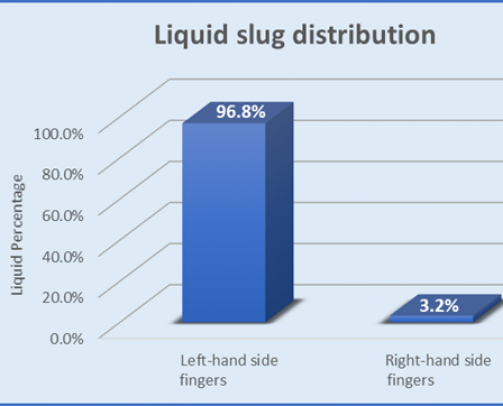
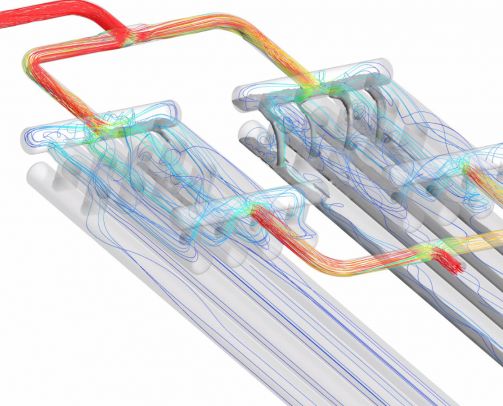
Benefit Analysis:
- Elimination of unplanned liquid level triggers
- Reduced production process interventions
- Increased production facility up time
- Increased production and revenue
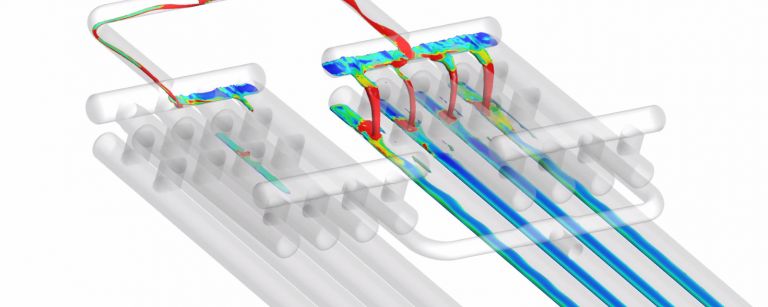
Interested?
Are you looking for troubleshooting, root cause analysis, debottlenecking or capacity increase of your equipment?